Vibrating screen mesh is a metal mesh structure element used for screening and filtering. It is widely used in screening, filtering, dehydration, desludging and other operations in many industries such as mining, coal mining, construction, glass factories, petroleum, hardware products, food processing, and medicine. It uses vibration waveforms to screen and classify materials on the screen to achieve separation of different particle sizes.
The weaving structure of the vibrating screen is diverse, including bidirectional corrugated bend, locking bend, bidirectional wave separation bend, flat top bend, unidirectional corrugated bend, etc. These structures make the screen strong and durable, able to withstand the huge impact and friction when the vibrating screen is working. The models and specifications of the screen are also diverse, such as flat screen plates, curved screens, etc., to meet the needs of different industries and application scenarios.The correct installation method of the vibrating screen is very important to ensure the screening effect and the service life of the screen.
Vibrating screen mesh installation methods
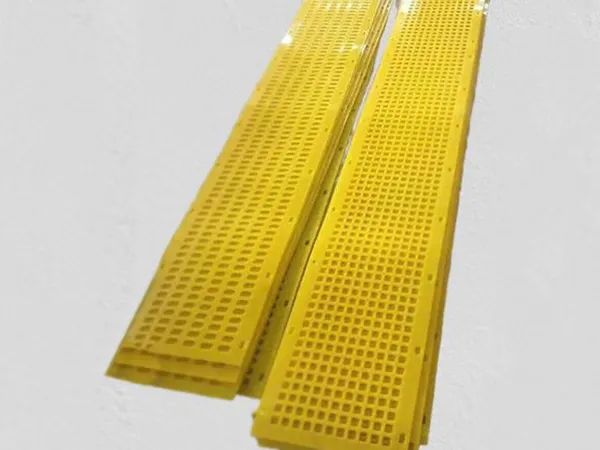
1. Preliminary preparation
Check the screen: Make sure the screen is not damaged or deformed, and the size matches the screen frame.
Prepare tools: Prepare the tools required for installation, such as bolts, nuts, hooks, wooden wedges, hammers, etc.
Clean the screen frame: Clean the debris and residue on the screen frame to ensure that the surface of the screen frame is clean and free of impurities.
2. Installation steps
Open the dust cover and take out the screen frame: First, you need to open the dust cover of the vibrating screen, and then take out the screen frame that needs to be replaced or installed.
Fix the screen:
Bolt fixation: For screen plates with a thickness greater than 8mm or textile screens with a large screen wire diameter, bolts can be used to fix them directly to the screen frame. Bolts are in the form of U-type and J-type. J-type bolts are more convenient to disassemble, so they are more commonly used.
Hook tensioning: For woven screens or screen plates with a thickness of less than 6mm, the end of the screen or screen plate can be bent into a hook shape, and then fixed with hooks and bolts. In order to effectively tension the screen surface and not produce secondary vibration, the bolts should be designed in a certain angle and elastic washers should be added on the outside.
Slot structure: Some vibrating screens use slot structure to fix the screen plate. This method is easy to disassemble and replace, and is fast. It is suitable for thin steel plate punching screen surface, rubber and polyurethane screen surface for medium material screening.
…
For more detailed information about vibrating screen mesh installation, please click here: https://www.zexciter.com/en/a/news/vibrating-screen-mesh-installation-methods.html