Introduction
In the face of escalating environmental concerns and the growing need for sustainable solutions, innovative technologies have emerged to address pressing issues like waste management and resource conservation. One such groundbreaking invention is the briquetting machine, a powerful tool designed to convert diverse types of waste materials into compact, eco-friendly briquettes. This technological marvel not only aids in waste reduction but also contributes significantly to the conservation of natural resources and the mitigation of environmental pollution.
Understanding Briquetting Machines
Briquetting machines are mechanical devices engineered to compress and compact a wide array of materials, ranging from biomass and agricultural residues to industrial and household waste. These machines utilize high pressure and temperature to bind these materials into uniform, dense briquettes, often cylindrical or square in shape. The resulting briquettes serve as efficient fuel sources and raw materials for various industrial processes.
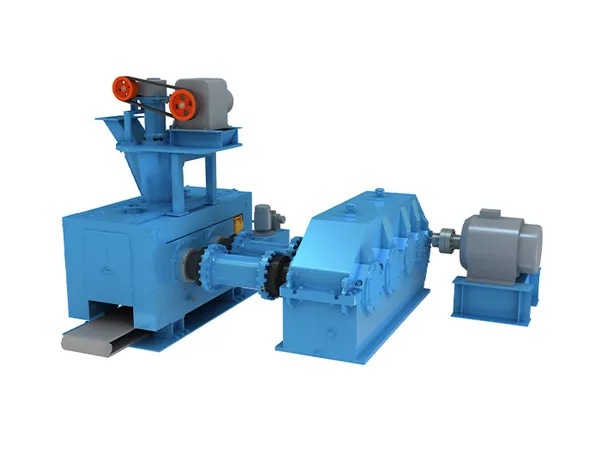
Key Components and Working Principle
Briquetting machines consist of several essential components, including a feeding system, a compression chamber, a hydraulic or mechanical press, and an ejection system. The process begins with the feeding of raw materials into the machine. Inside the compression chamber, high pressure and, in some cases, heat are applied, causing the materials to undergo a transformation at the molecular level. This results in the formation of sturdy, energy-dense briquettes. The ejection system then releases the briquettes, ready for use or further processing.
Applications and Environmental Benefits
Biomass Briquettes for Clean Energy:
Briquetting machines play a pivotal role in the production of biomass briquettes, which serve as a clean and renewable energy source. These briquettes find applications in industrial boilers, domestic heating, and various thermal processes, reducing reliance on fossil fuels and lowering greenhouse gas emissions.
Waste Recycling and Environmental Conservation:
Briquetting machines offer an effective solution for managing various types of waste, such as agricultural residues, paper, plastic, and metal shavings. By converting these waste materials into briquettes, the machines facilitate easier handling, transportation, and storage, thereby reducing environmental pollution and landfills.
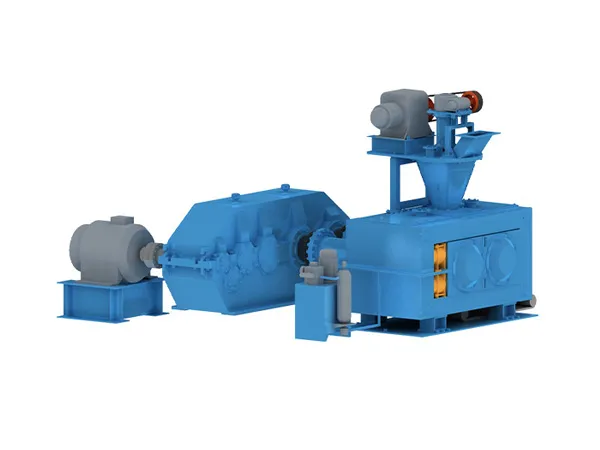
Advantages of Briquetting Machines
Waste Reduction: Briquetting machines significantly reduce the volume of waste materials, enabling efficient storage, transportation, and handling.
Energy Efficiency: Briquettes serve as an energy-dense fuel source, providing a cleaner and more sustainable alternative to traditional fuels.
…
For more detailed information about the briquetting machine, please click here: https://www.zymining.com/en/a/news/introduction-to-briquetting-machine.html